Revolutionizing Manufacturing with Industry 4.0 & IoT Solutions: Challenges & Opportunities
Industry 4.0 technology and the Internet of Things (IoT) based solutions are revolutionizing the way manufacturing companies operate. Businesses now have the chance to develop cutting-edge, integrated technology thanks to the Internet of Things. This paves the way for the creation of innovative, IoT-based solutions. The Internet of things enables the use of advanced technologies to create Industry 4.0 solutions.
According to a McKinsey & Company study, the typical value captured by successfully implementing Industry 4.0:
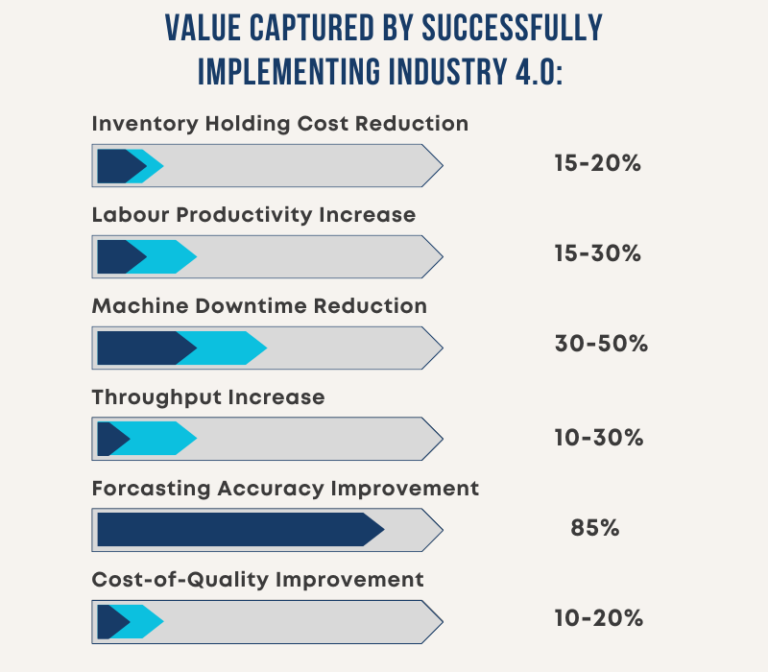
The Internet of Things (IoT) is playing a critical role in the evolution of the manufacturing sector by enabling the automation and optimization of various processes. Here are a few ways in which IoT is assisting the manufacturing sector:
- Predictive maintenance: Sensors can be used to monitor machines and equipment in real-time, Processing, aggregation, and correlation of sensor data over time allows manufacturers to identify potential problems before they occur. This approach, known as predictive maintenance, can reduce unplanned downtime, minimize inventory, and repair costs.
- Improved efficiency: By connecting various machines and devices through IoT, manufacturers can create a more efficient and streamlined production process. For example, Productivity leaks can be blocked by monitoring machine downtime and material handling operations.
- Enhanced quality control: IoT is used to digitize measurements of products at every stage of production, from raw materials to finished goods. This helps manufacturers to identify defects early on and make quick & timely adjustments to improve product quality.
- Remote monitoring: Creating a digital twin of a machine and production process allows manufacturers to remotely monitor production processes, transitioning to data-based organization than person-based organization and enabling greater flexibility in manufacturing operations.
- Data analytics: A large volume of data generated is used for long term analysis to gain valuable insights into production processes, quality, material handling and supply chain performance. This data is used to optimize processes and improve overall efficiency.
What are the common pitfalls of scaling these Industry 4.0 and IoT solutions?
Most manufacturing companies remain stuck in pilot purgatory, struggling to capture the full potential of their transformation efforts or deliver a satisfactory return on investment. Manufacturing companies must carefully consider these challenges and develop a comprehensive plan to overcome them to successfully adapt to Industry 4.0 and IoT solutions
- Manufacturing companies consider Industry 4.0 technology as a cure for all problems on the shop floor. Thus, the expectations and result always mismatch. Every industry may have different pain areas that need an application of suitable technology and analysis.
- Many manufacturing companies still rely on legacy systems that are not compatible with Industry 4.0 and IoT solutions. Upgrading these systems can be expensive and time-consuming.
- IoT devices generate a vast amount of data that needs to be collected, stored, and processed. Ensuring the privacy and security of this data is critical to prevent cyber-attacks and protect sensitive information.
- Implementing and maintaining Industry 4.0 solutions requires specialized skills and knowledge in IT-OT integration, which may not be available within manufacturing company. Training existing staff or hiring new personnel with the required skills can be a challenge.
- Many companies use multiple software and hardware systems that need to be integrated to function effectively. Integrating these systems can be complex and require a significant amount of time and resources.
- Some employees and stakeholders may be resistant to change, particularly if they are used to working with traditional systems. Overcoming this resistance can be a challenge, but it is essential to ensure the successful adoption of Industry 4.0 solutions.
How can manufacturing companies get the best out of Industry 4.0?
To gain a competitive edge in Industry 4.0, manufacturers need to adopt a more strategic and value-driven approach when using IoT technologies. Here are a few ways in which this can be achieved:
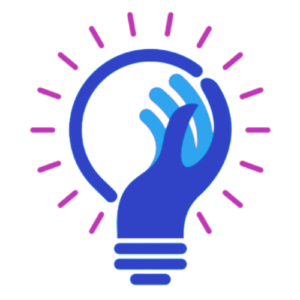
Focus on Business Outcomes:
Instead of just deploying IoT technologies for the sake of innovation, manufacturers should focus on two or three specific business outcomes, high priority pain areas such as reducing costs, improving quality, or increasing efficiency. This will help ensure that IoT investments deliver tangible value to the organization.
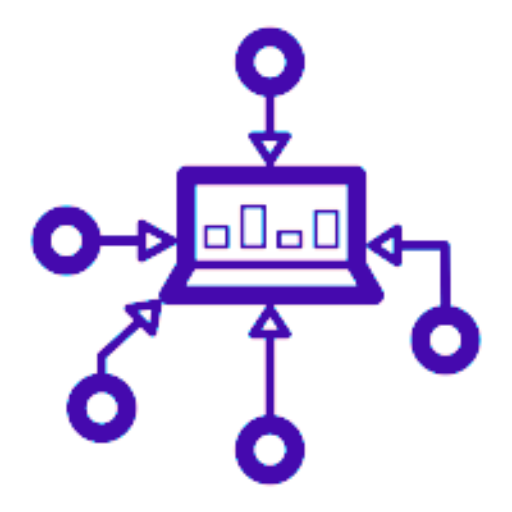
Data Integration & Analysis:
IoT generates vast amounts of data, but this data is only valuable if it can be integrated and analyzed effectively i.e., transforming data into information. Manufacturers should not shy away from investing in tools and platforms that enable data integration and analysis, such as data lakes and machine learning algorithms. This will help manufacturers gain insights into their operations and identify areas for improvement.
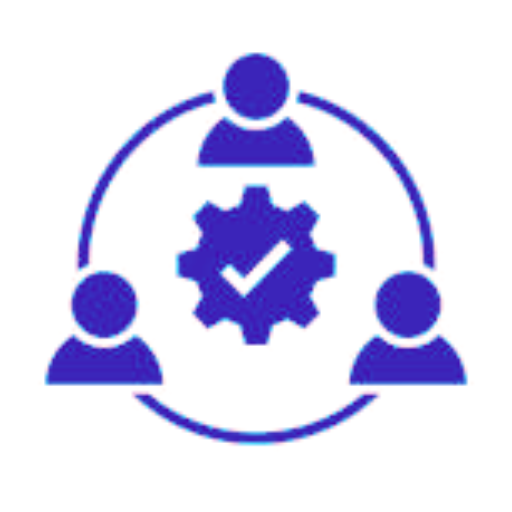
Collaboration & Partnership:
Manufacturing sector is tuned for supplier-vendor relationship. Openness to collaborate with IoT technology providers, system integrators, and other partners to co-create solutions that meet their specific needs. This will help ensure that IoT solutions are tailored to the unique requirements of the manufacturing organization.
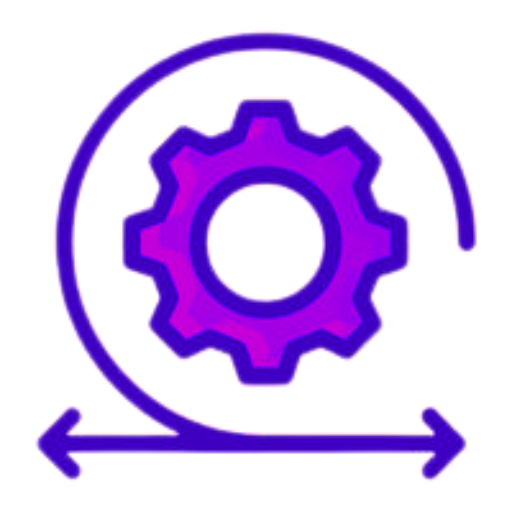
Agile Approach to Deployment:
IoT technologies are evolving rapidly, and manufacturers need to be agile in their deployment strategies. This means adopting an incremental approach to IoT deployment, where individual components can be added as needed. This will help manufacturers keep pace with the rapidly changing IoT landscape.
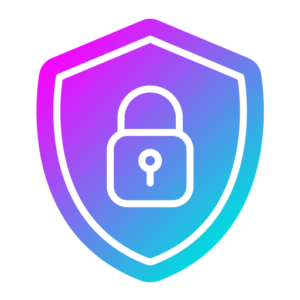
Cyber Security & Risk Management:
As manufacturers become more reliant on IoT technologies, they also face greater cybersecurity and risk management challenges. Manufacturers should invest in robust cybersecurity and risk management strategies to protect their operations from cyber threats and other risks.
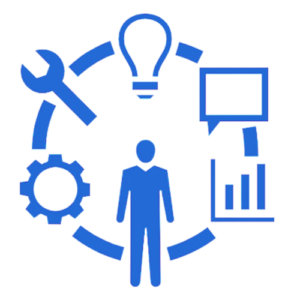
Infrastructure Readiness:
Success of Industry 4.0 solutions is also driven by the capability of underlying infrastructure. This includes machine readiness, network capacity and computing capacity.
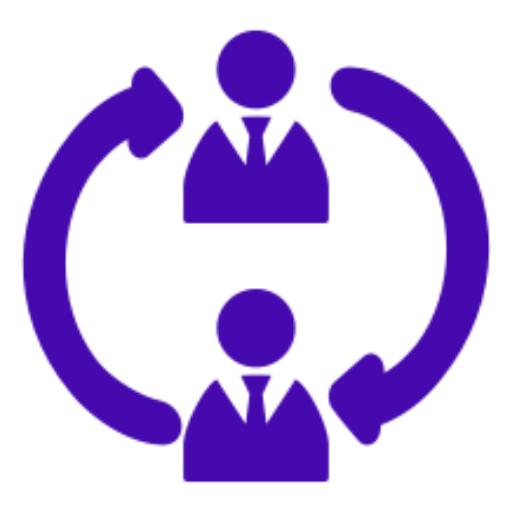
Change Management:
It is critical to take all layers of folks in the organization together in adopting Industry 4.0. Having a right intent by a business owner with clear communication helps in alignment leading to support from all in driving this change.
By adopting a more strategic and value-driven approach to IoT, manufacturers can gain a competitive edge in Industry 4.0. If you are manufacturer and looking for an IoT based solutions, then contact Us: